CEMENT INDUSTRY
India is the second-largest producer of cement in the world. Its market share is more than 8% of globally. India has a lot of potential for development in the infrastructure and construction sector and the cement sector is expected to largely benefit from it. Infrastructural development led to high demand of cement in India. Polypick UHMW PE is being used at various stages of cement production.
Raw Material Extraction/Quarry
The raw cement ingredients needed for cement production are limestone (calcium), sand and clay (silicon, aluminium, iron), shale, fly ash, mill scale, and bauxite. The ore rocks are quarried and crushed into smaller pieces of about 6 inches. Secondary crushers or hammer mills then reduce them to an even smaller size of 3 inches. After that, the ingredients are prepared for pyro-processing.
Glider Idlers, being as low wear material, are used for transporting the raw material through conveyor belts. All the raw material are highly corrosive and will corrode the metal rollers and idlers frequently. With Glider, the replacement is very less and it can survive easily with corrosive material like lime stone, fly ash and bauxite.
Polypick Truck bed liners are also cost effective and safe method to transport corrosive raw material. It not only increases the life of truck body, but also safe guard the workers during unloading the material. The smooth flow and anti-sticking property of Polypick Polymer Liners does not allow material to stick on the top of dumpers and saves from fatal accidents.
Grinding, Proportioning, and Blending
The crushed raw ingredients are made ready for the cement-making process in the kiln by combining them with additives and grinding them to ensure a fine homogenous mixture. The composition of cement is proportioned here depending on the desired properties of the cement. Generally, limestone is 80%, and the remaining 20% is clay. In the cement plant, the raw mix is dried (moisture content reduced to less than 1%); heavy wheel-type rollers and rotating tables blend the raw mix and then the roller crushes it to a fine powder to be stored in silos and fed to the kiln.
All the material are conveyed through hoppers and conveyors. The hoppers again required lining of anti-corrosive, non-sticky, low wear material – POLYPICK. Smooth flow from hoppers requires UHMW PE liners to be fixed in hoppers. The bunkers, Silos require to store the raw material has to be lined with Polypick to avoid clogging. Once the material is preheated and moved to klin for final production, cooling and final grinding is done.
Packing and Shipping
Cement is then conveyed from grinding mills to silos (large storage tanks) where it is packed in 25-50 kg bags. Most of the product is shipped in bulk quantities by trucks, trains, or ships. The storage of final cement also need UHMW PE lined silos.
Further for packing the cement in bags, the entire track of packed cement bag is lined with Polypick UHMW PE sheets as shown in picture and video. Cement being corrosive in nature, reduces the life of metal. Polypick Liners provides smooth flow of cement bags and gives long life.
UHMW PE (Ultra-High Molecular Weight Polyethylene) products are widely used in cement plants due to their excellent properties such as high abrasion resistance, low friction, and chemical inertness. Here’s a comprehensive overview of UHMW PE applications in cement plants:
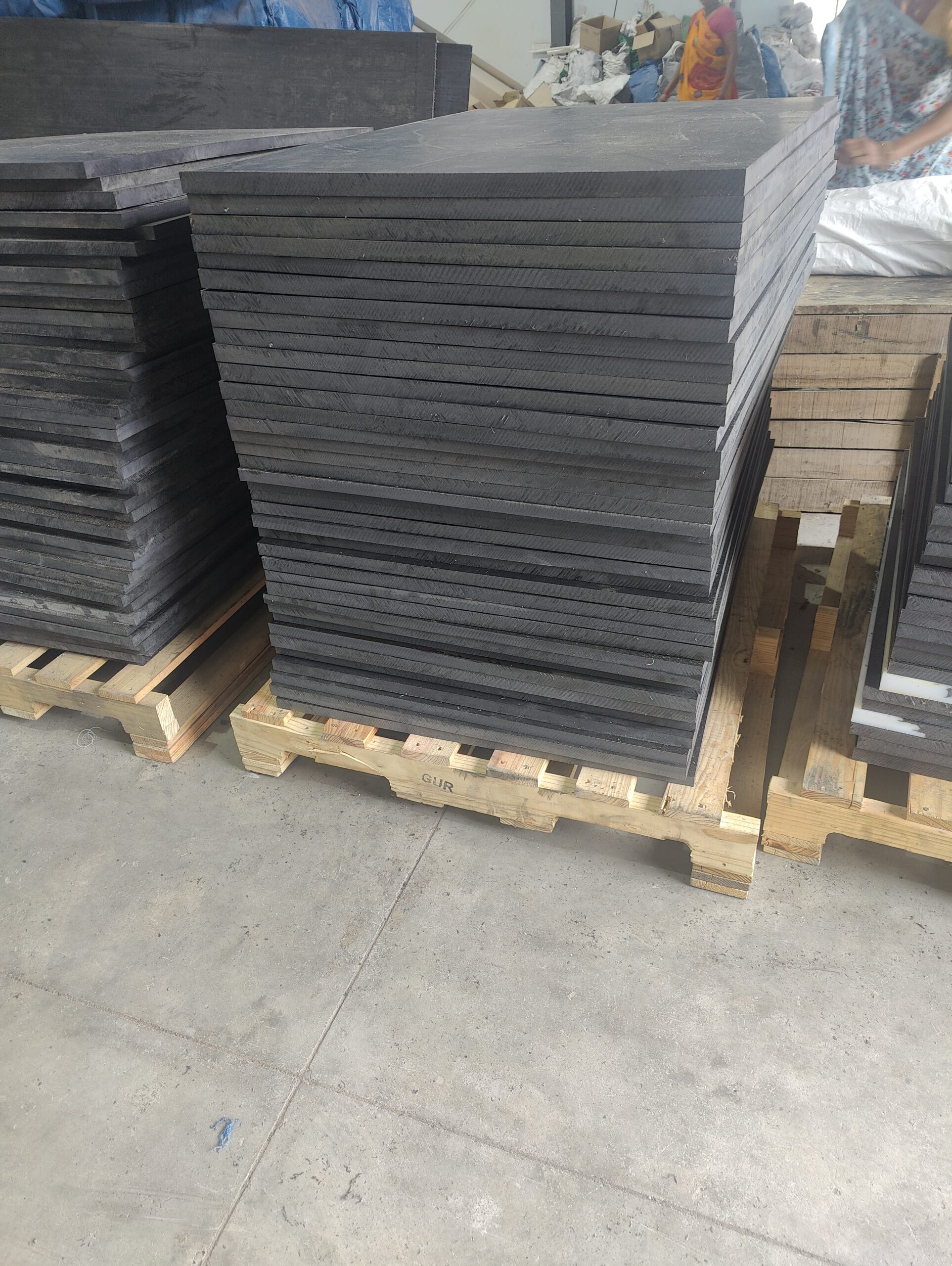
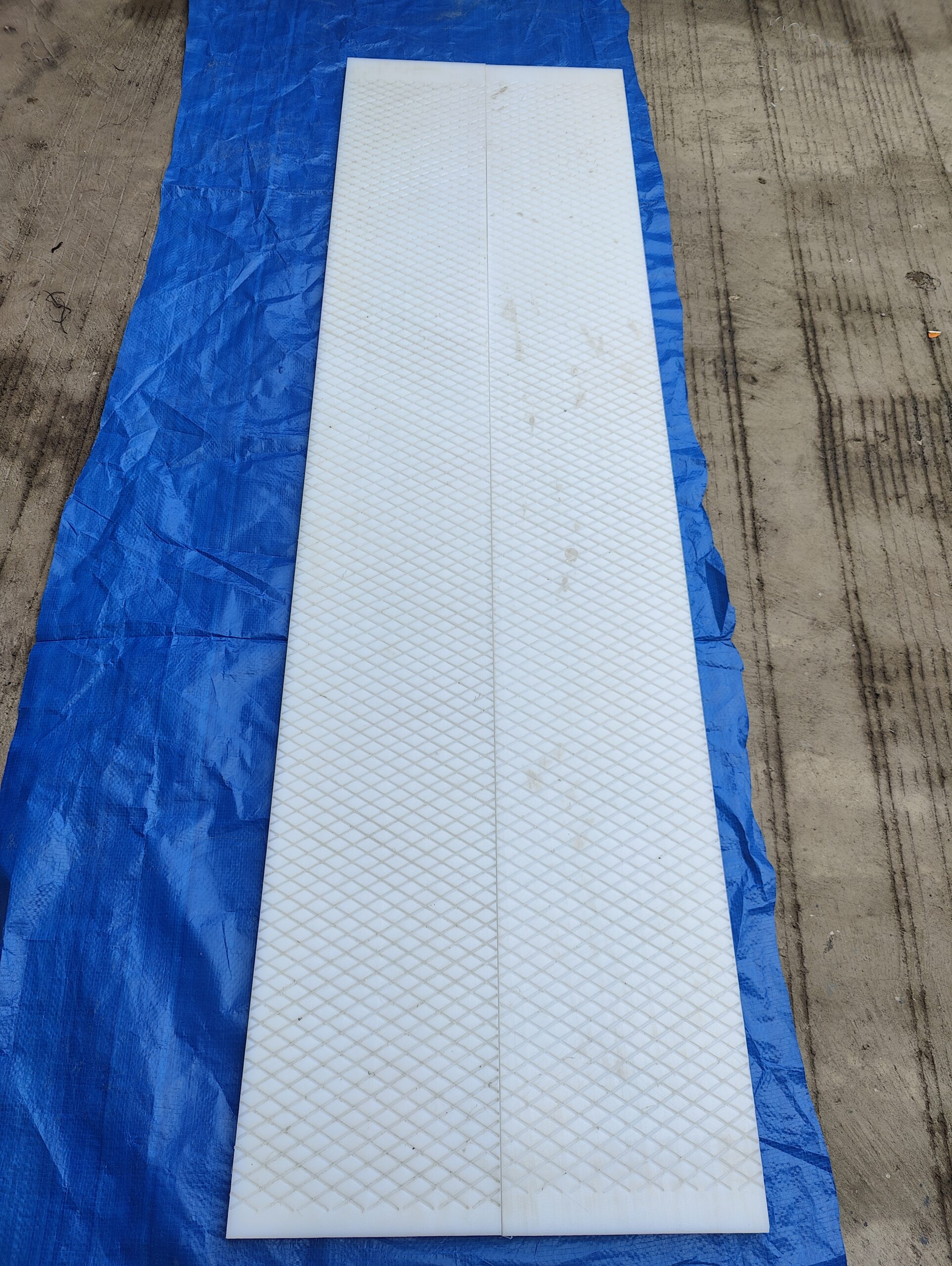
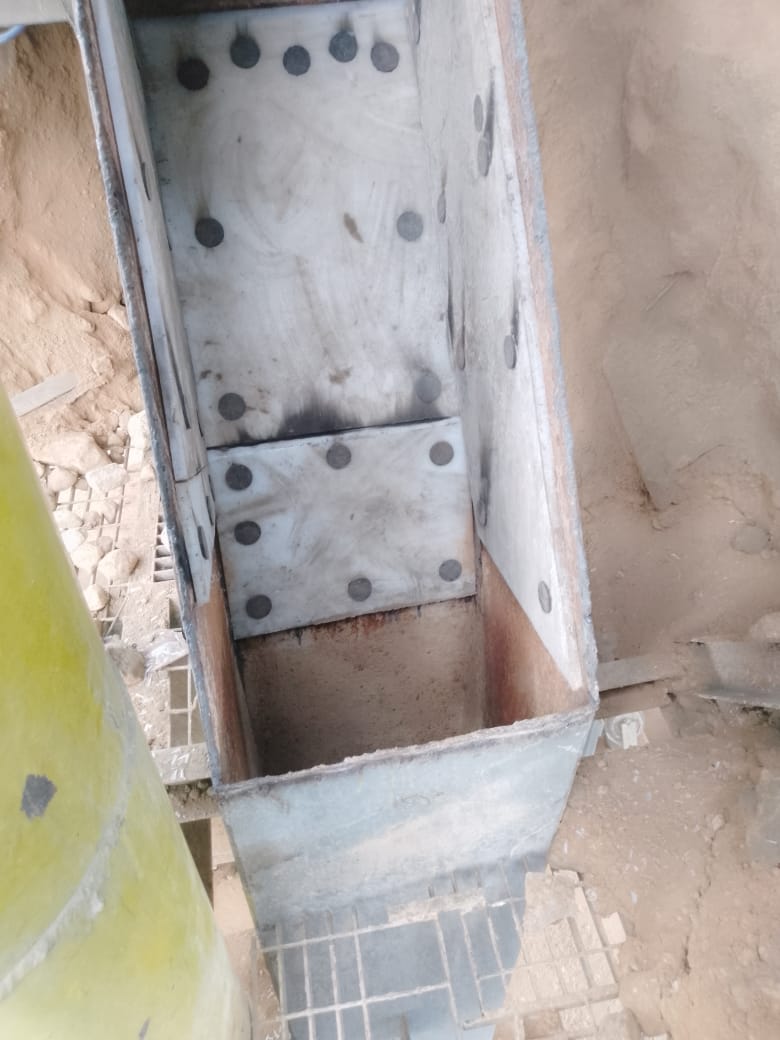
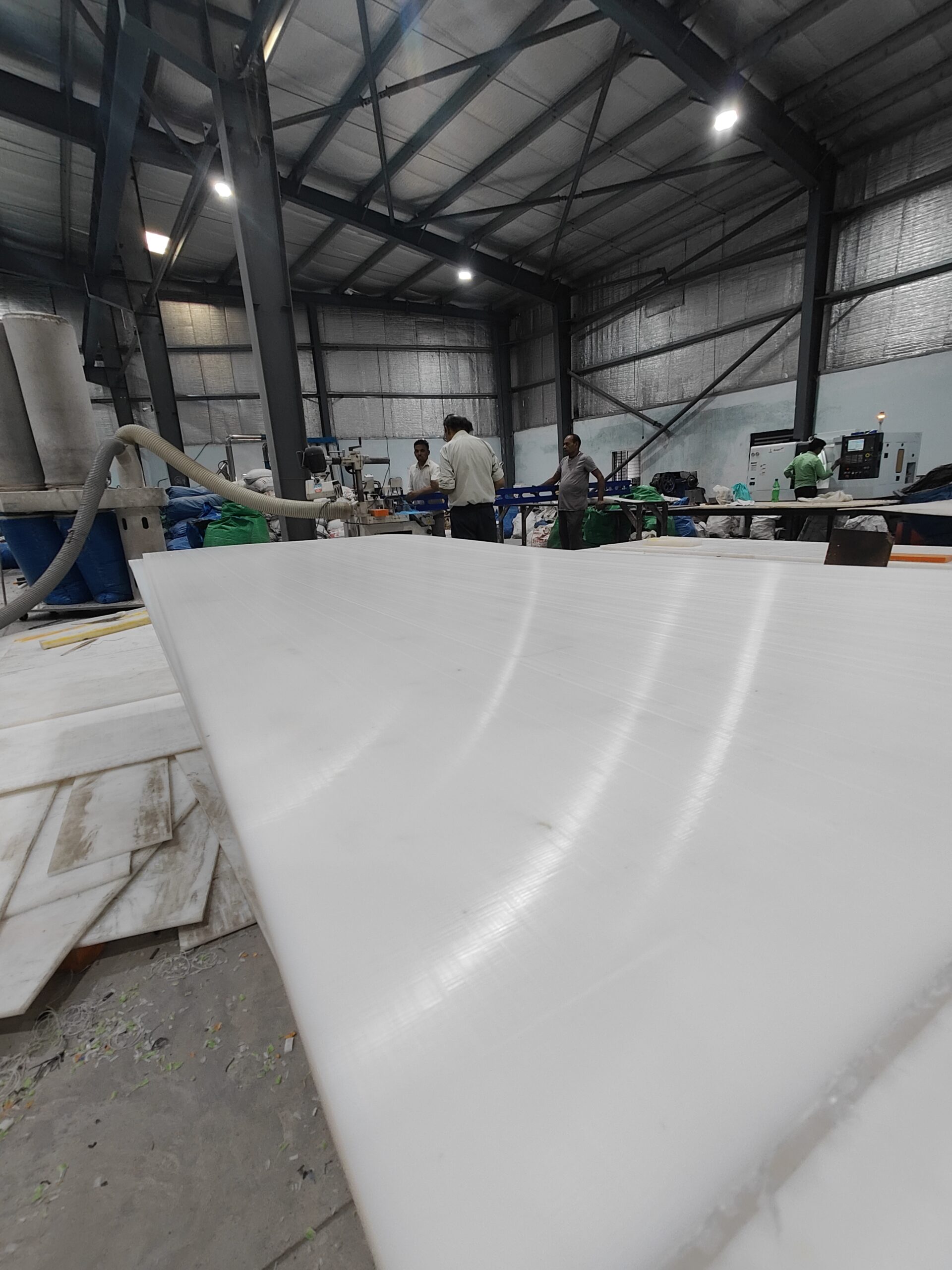
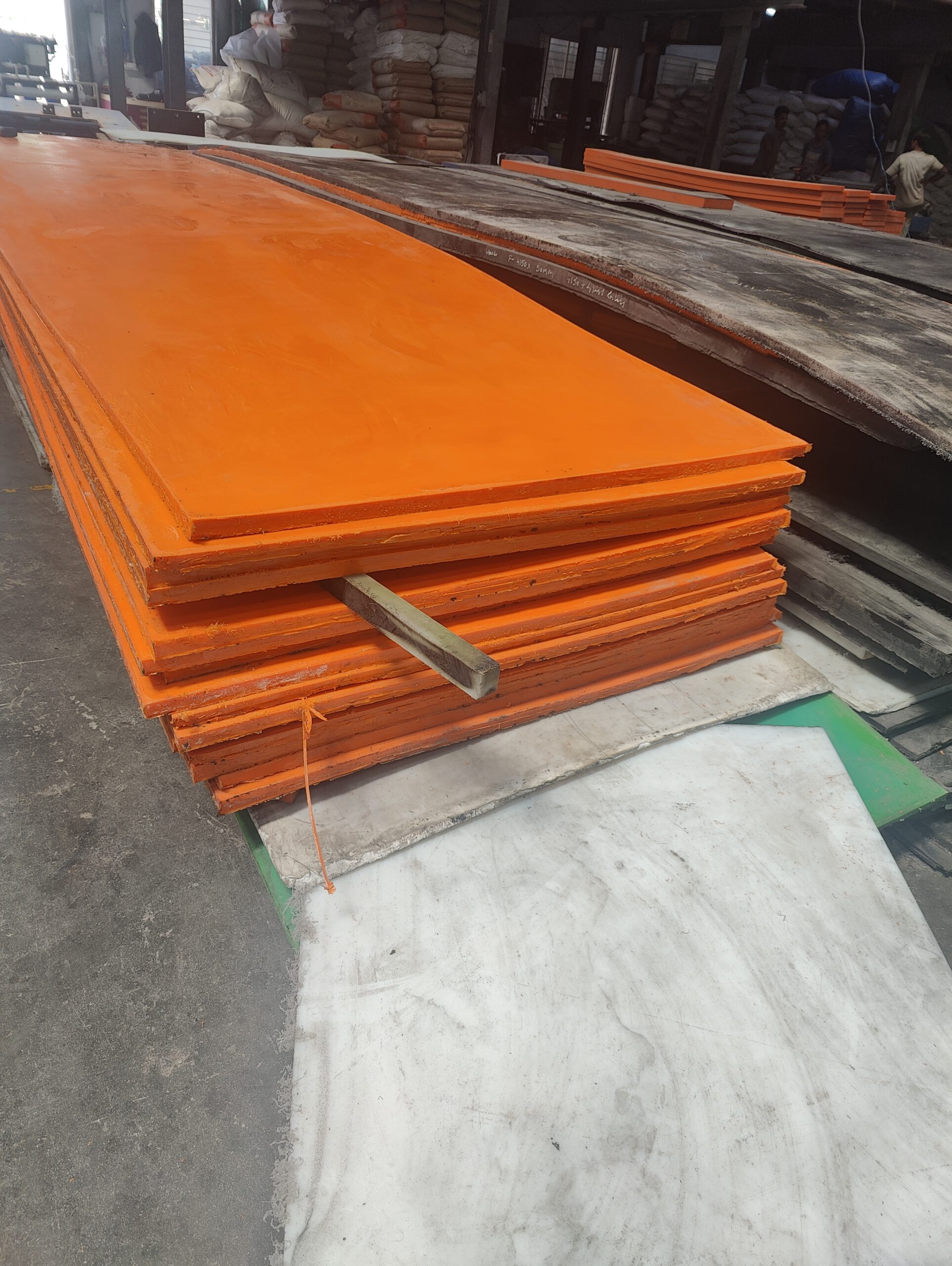
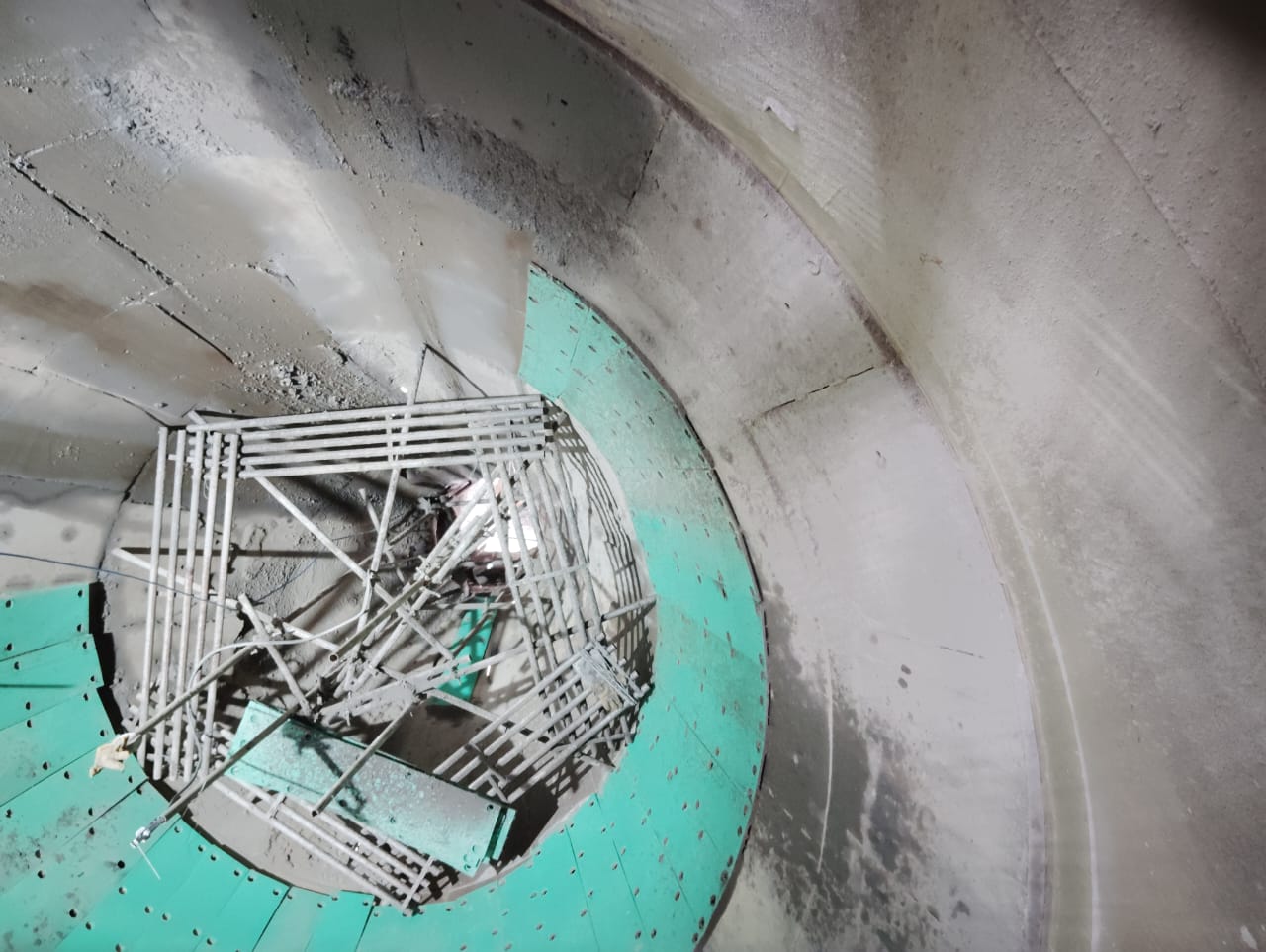
1. Material Handling Systems:
a) Conveyor Components:
- Glider Idlers and rollers for raw material and clinker conveyors.
- Skirting to contain dust and material spillage.
- UHMW PE Wear strips and guide rails.
- Impact beds in transfer points.
b) Chute Linings:
- Lining for raw material, clinker, and cement chutes.
- Improves material flow and reduces wear.
c) Hopper and Bin Linings:
- Facilitates material flow in storage hoppers and bins.
- Prevents material buildup and bridging.
d) Truck/Rail Car Linings:
- Linings for material transport vehicles to ease unloading.
2. Grinding and Milling:
a) Mill Linings:
- Wear-resistant linings for ball mills and vertical roller mills.
b) Separator Components:
- Wear parts in air classifiers and separators.
3. Cement Packaging:
a) Bagging Plant Components:
- Guide rails and wear strips in bagging machines.
- Chute linings in packing plants.
b) Palletizing Equipment:
- Wear components in palletizers and wrapping machines.
4. Maintenance and Safety:
a) Outrigger Pads:
- For mobile equipment stability during maintenance.
b) Walkway Surfaces:
- Non-slip, corrosion-resistant walkway materials.
c) Protective Guards:
- Machine guards and safety barriers.
5. Environmental Control:
a) Water Treatment:
- Parts in water filtration and treatment systems.
6. Quarry Operations:
a) Screening Equipment:
- Screen panels and wear liners in aggregate screening.
b) Crusher Components:
- Wear liners in crushers and grinding equipment.
Benefits of UHMW PE in Cement Plants:
1. Abrasion Resistance:
- Extends equipment life in highly abrasive cement environments.
2. Low Friction:
- Improves material flow, reduces power consumption.
3. Impact Resistance:
- Withstands heavy loads and impacts common in cement processing.
4. Dust Control:
- Helps contain and manage cement dust.
5. Noise Reduction:
- Dampens sound from material impacts and equipment operation.
6. Chemical Resistance:
- Withstands exposure to various chemicals used in cement production.
7. Lightweight:
- Easier to handle and install compared to metal components.
8. Self-Lubricating:
- Reduces need for additional lubrication in many applications.
9. Non-Stick Properties:
- Prevents material buildup, reducing maintenance needs.
Design Considerations:
1. Thickness Selection:
- Based on wear expectations and load requirements.
2. Attachment Methods:
- Mechanical fastening, adhesive bonding, or custom-designed systems.
3. Temperature Limitations:
- Not suitable for very high-temperature areas (e.g., near kilns).
4. UV Resistance:
- For outdoor applications, UV-stabilized grades should be used.
5. Static Dissipation:
- In dust-sensitive areas, antistatic grades may be necessary.
Implementation and Maintenance:
1. Regular Inspection:
- Scheduled checks for wear and damage.
2. Cleaning Protocols:
- Procedures for removing cement buildup.
3. Replacement Strategy:
- Planned replacement to minimize downtime.
4. Performance Monitoring:
- Tracking wear rates and efficiency improvements.
Limitations:
- Not suitable for extremely high-temperature zones.
- May require more frequent replacement in severe abrasive conditions.
- Load-bearing capacity limitations compared to some metal alternatives.
UHMW PE products play a crucial role in improving efficiency, reducing maintenance costs, and enhancing safety in cement plants. Their use is particularly valuable in areas with high wear, where material flow is critical, and where dust containment is essential.