Paper Industry
UHMW PE (Ultra-High Molecular Weight Polyethylene) dewatering elements play a crucial role in the paper and asbestos industries, particularly in the dewatering processes. These elements are designed to remove excess water from the material being processed, improving efficiency and product quality. Let’s explore their application in both industries:
1. UHMW PE Dewatering Elements in the Paper Industry:
Applications:
a) Foils and Blades:
- Used on the forming section of paper machines.
- Help in initial water removal from the paper web.
b) Dewatering Shoes:
- Placed under the forming fabric to enhance water removal.
c) Suction Box Covers:
- Cover the vacuum boxes in the forming section.
d) Doctor Blades:
- Used to clean and dewater rolls in various sections of the paper machine.
Benefits:
- Excellent wear resistance, extending service life.
- Low friction, reducing drag on the paper web.
- Chemical resistance to withstand harsh papermaking chemicals.
- Non-stick properties, preventing fiber buildup.
- Customizable designs to fit specific machine requirements.
Design Considerations:
- Profile shape optimized for efficient water removal.
- Mounting systems for easy installation and replacement.
- Surface finish to balance dewatering efficiency and fabric wear.
2. UHMW PE Dewatering Elements in the Asbestos Industry:
Applications:
a) Filter Press Plates:
- Used in filter presses to separate asbestos fibers from liquid slurry.
b) Drainage Elements:
- Incorporated into dewatering equipment to remove water from asbestos-containing materials.
c) Conveyor Components:
- Dewatering sections on conveyor systems handling wet asbestos materials.
Benefits:
- Chemical resistance to withstand aggressive chemicals used in asbestos processing.
- Abrasion resistance for handling abrasive asbestos fibers.
- Non-stick properties to prevent material buildup.
- Easy to clean, reducing contamination risks.
- Compliant with safety regulations for handling hazardous materials.
Design Considerations:
- Optimized perforation patterns for efficient water drainage.
- Sealed edges to prevent fiber intrusion into the material.
- Smooth surfaces to facilitate material release and cleaning.
Common Advantages in Both Industries:
1. Durability:
- Long-lasting performance in wet and abrasive environments.
2. Improved Dewatering Efficiency:
- Engineered profiles and surfaces enhance water removal.
3. Reduced Maintenance:
- Longer service intervals compared to metal alternatives.
4. Energy Savings:
- Lower friction leads to reduced energy consumption in processing.
5. Product Quality:
- Consistent dewatering performance improves end-product quality.
6. Safety:
- Non-corrosive and splinter-free, reducing workplace hazards.
7. Customization:
- Can be tailored to specific machine designs and process requirements.
Implementation Considerations:
1. Installation:
- Often designed for easy retrofitting into existing equipment.
2. Monitoring:
- Regular inspection for wear and performance optimization.
3. Cleaning:
- Periodic cleaning to maintain optimal performance.
4. Replacement Strategy:
- Planning for timely replacement to maintain process efficiency.
5. Material Grade Selection:
- Choosing the appropriate UHMW PE grade based on specific application demands.
Limitations:
- Temperature limitations (not suitable for very high-temperature processes).
- May require more frequent replacement in extremely abrasive conditions.
UHMW PE dewatering elements offer significant advantages in both the paper and asbestos industries, contributing to improved process efficiency, product quality, and equipment longevity. Their use is particularly valuable in these industries due to the challenging wet and abrasive environments typical in dewatering processes.
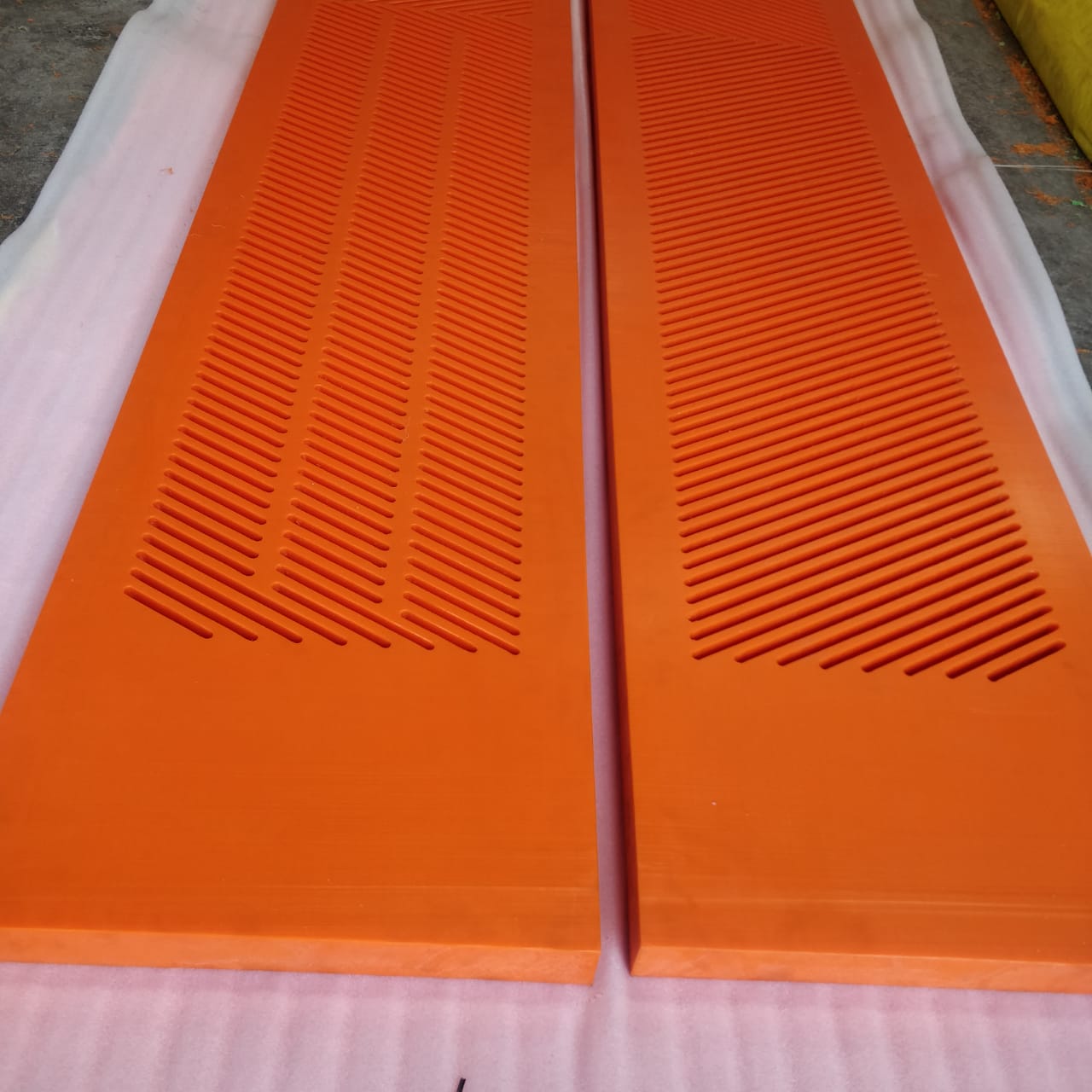
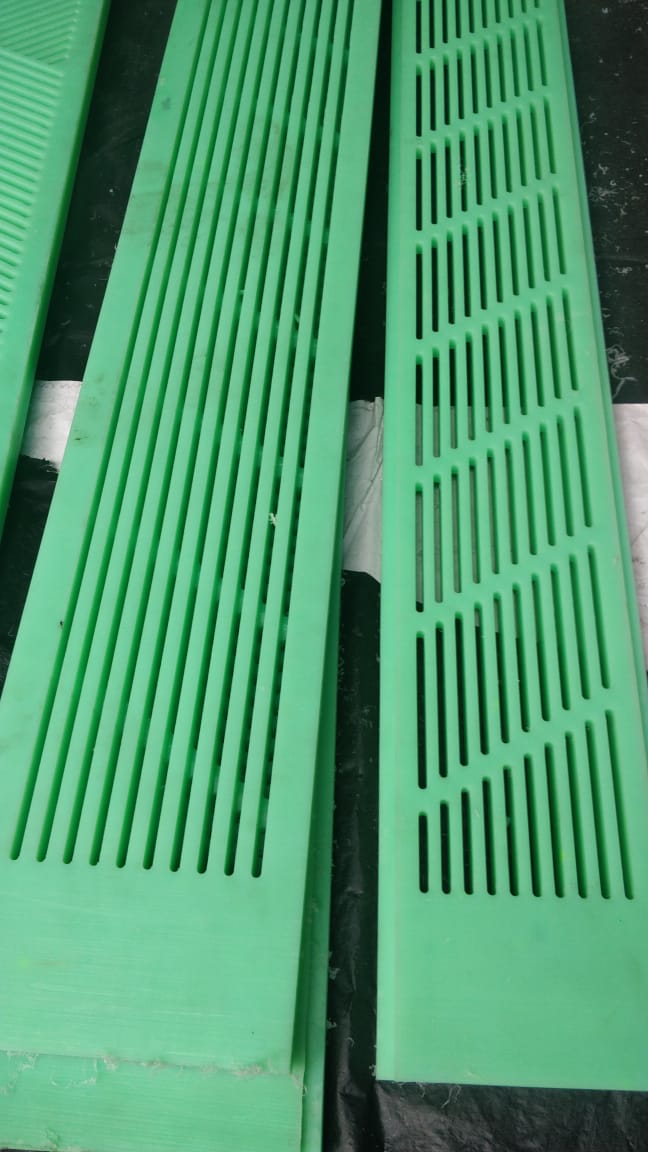
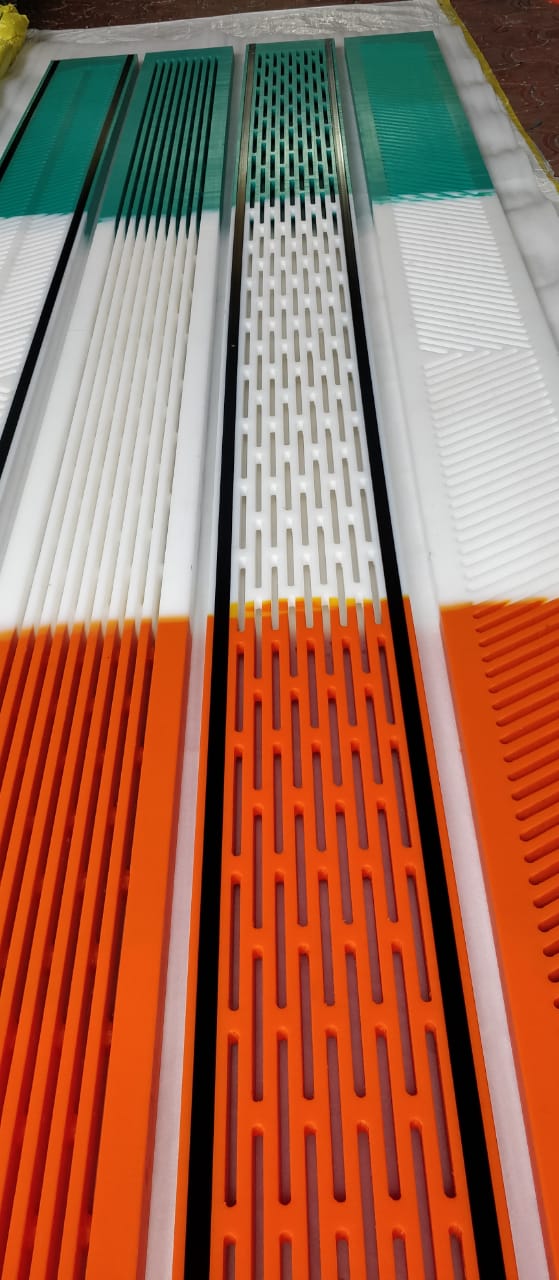
GRADES OF POLYTRON UHMW PE PRODUCTS:
UHMWPE grades primarily depend on its Molecular Weight. Poly Ethylene, which has got molecular weight more than 3 Million, falls under the family of UHMW PE. Few Additives can also be added to enhance the properties of UHMWPE components depending upon the application.
We @ POLYTRON, keeps the range of UHMW PE to suit the particular requirement and budget.
POLYPICK Grade:
The base material is having the molecular weight of 3 to 5 Million, which is widely used in general engineering application. The application in this category is not so demanding and basic properties of UHMW PE needed to be explored. The raw material is homogenous and sourced from trusted and verified manufacturers.
POLYTRON VIRGIN:
We manufacture 5.5 to 6.8 Million molecular weight material in this grade. Only few, prominent companies world-wide produces it. We have kept our standard material as 6.8 Million to maintain the quality. This is sourced from USA origin and has got the best quality.
POLYTRON PLUS:
There are quite a few applications where material should have low co-efficient of friction. The additives like Ceramic/Glass beads are added in Virgin Grade. These additives improve the hardness and improve wear properties.
G9:
G9 become a sub-brand of POLYTRON. Its quality and performance has set a benchmark in the industry. The people have started asking for G9 directly. Our G9 grade is a combination of 9.2 Million Molecular Weight material with special additives which make it a distinguish product in the market. Its performance is world class and processed under strict production parameters. This is being widely used in extreme conditions where you need to explore the true properties of UHMW PE.