Steel Industry
As India works towards becoming a manufacturing powerhouse through policy initiatives like Make in India, the steel industry has emerged as a major focus area given the dependence of a plethora of sectors on its output. India is currently the world’s second largest producer of steel and is set to become the second largest consumer of steel, with the industry contributing about 2% of the country’s GDP.
Steel is an alloy consisting primarily of iron and less than 2% carbon. Iron ore is, therefore, essential for steel production, which is essential in maintaining a strong industrial base. 98% of mined iron ore is used to make steel. Iron is one of the most abundant metallic elements. Its oxides, or ores, make up about 5% of the earth’s crust.
The integrated steelmaking route, based on the blast furnace (BF) and basic oxygen furnace (BOF), which uses raw materials including iron ore, coal, limestone and recycled steel. The electric arc furnace (EAF) route uses primarily recycled steels and direct reduced iron (DRI) or hot metal, and electricity.
The either method you use, Key raw materials needed in steelmaking include iron ore, coal, limestone and recycled steel.
Coking coal is a key raw material in steel production. As iron occurs only as iron oxides in the earth’s crust, the ores must be converted, or ‘reduced’, using carbon. The primary source of this carbon is coking coal. Coke, made by carburising coking coal (i.e. heating in the absence of oxygen at high temperatures), is the primary reducing agent of iron ore. Coke reduces iron ore to molten iron saturated with carbon, called hot metal.
Coal reserves are available in almost every country worldwide, with recoverable reserves in around 80 countries. Although the biggest reserves are in the US, China, Russia, Australia and India, coal is actively mined in more than 70 countries.
Polypick comes in the picture right from the beginning of excavating iron ore, coal and lime stone. Once the raw material is mined, it can be either transported by trucks/dumpers or conveyor system.
The POLYPICK – Truck Bed Liners not only solves the problem of sticking but gives a free flow to the material while unloading the truck. The low wear property of POLYPICK liners gives a longer life to the truck body.
If the material is being transported through belt conveyors, the GLIDER rollers and idlers are being used. This revolutionary idler not only gives better life, but also save the cost of frequent replacement.
Once the MS rolls are made, the Polypick logs are used to keep the rolls static are also being made of POLYPICK. This avoids the use of precious wood and a cost-effective solution.
The cold rolling mills used to reduce the thickness of metal sheet also uses Pressure Pads made of POLYPICK material. It avoids the metal-to-metal contact and has the longer life. Most of the companies are still using precious wooden blocks. POLYPICK UHMW PE pressure pads are the best cost-effective alternative to the Wood.
Pressure pads, often made from materials like UHMW PE (Ultra-High Molecular Weight Polyethylene) or other suitable polymers, play a significant role in various applications within the steel industry. Here’s an overview of their usage, focusing on UHMW PE pressure pads:
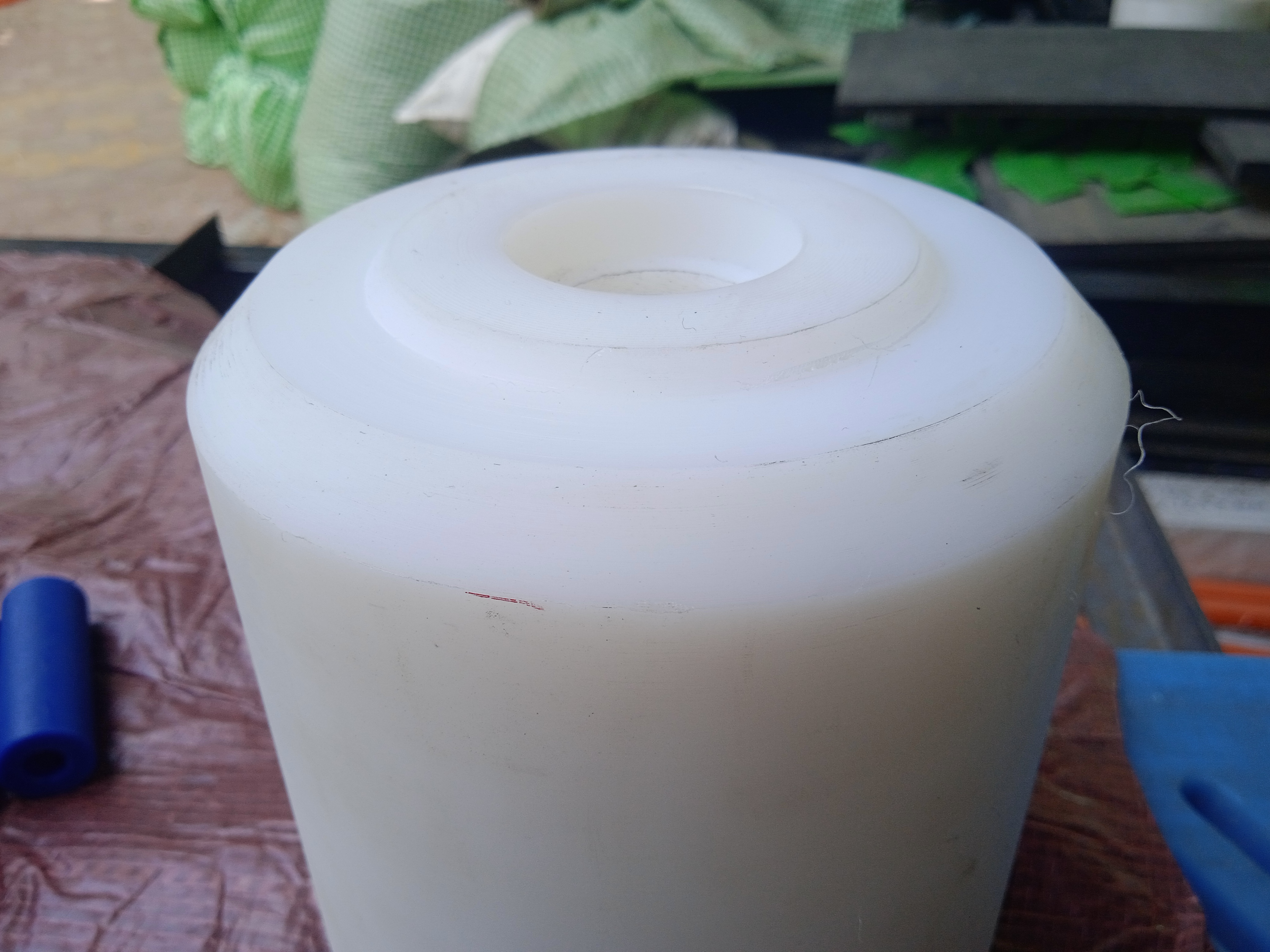
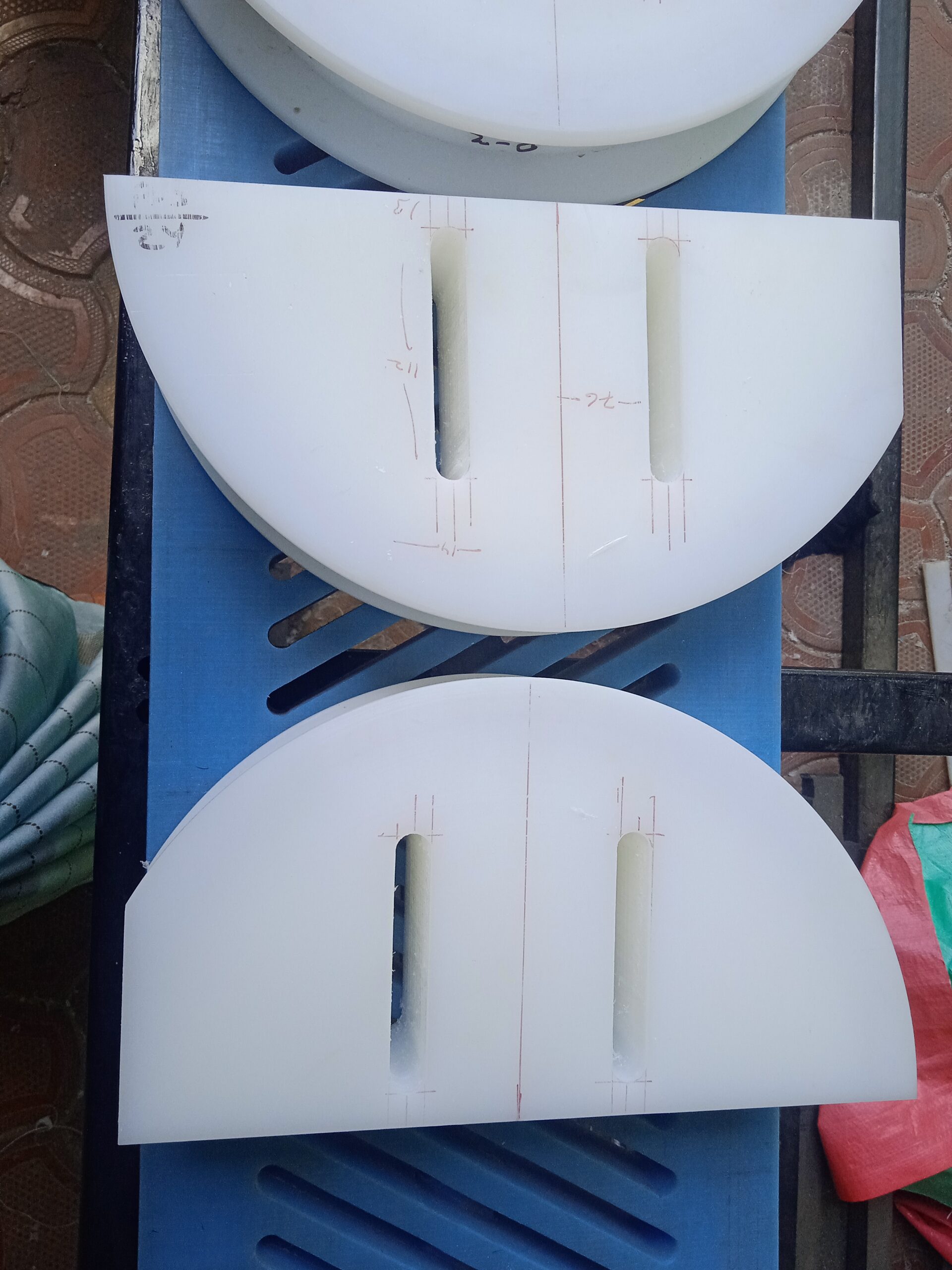
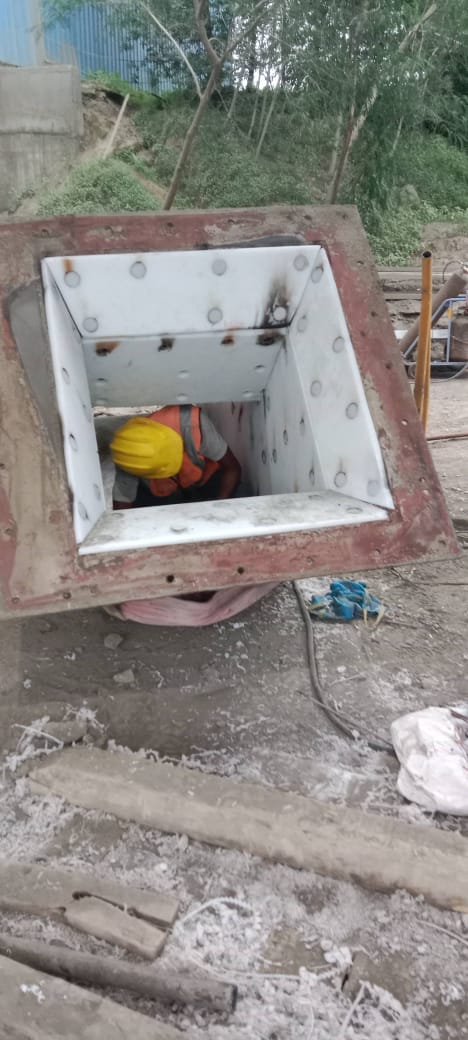
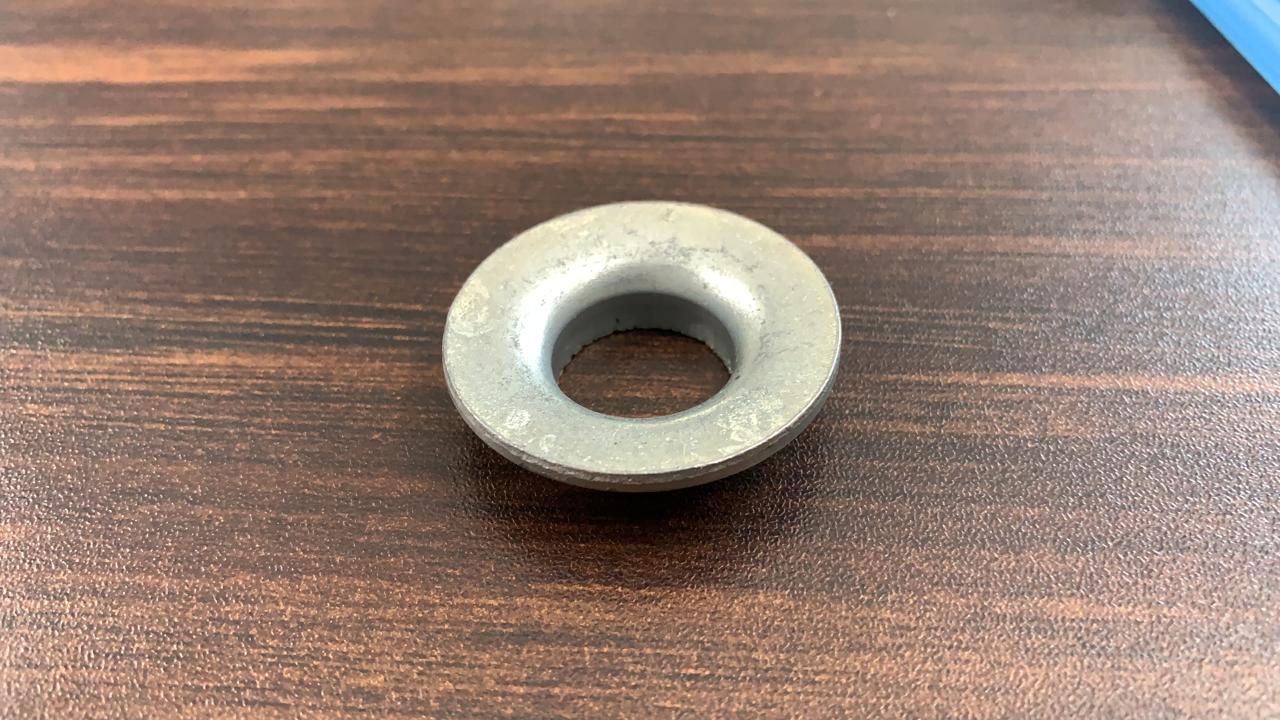
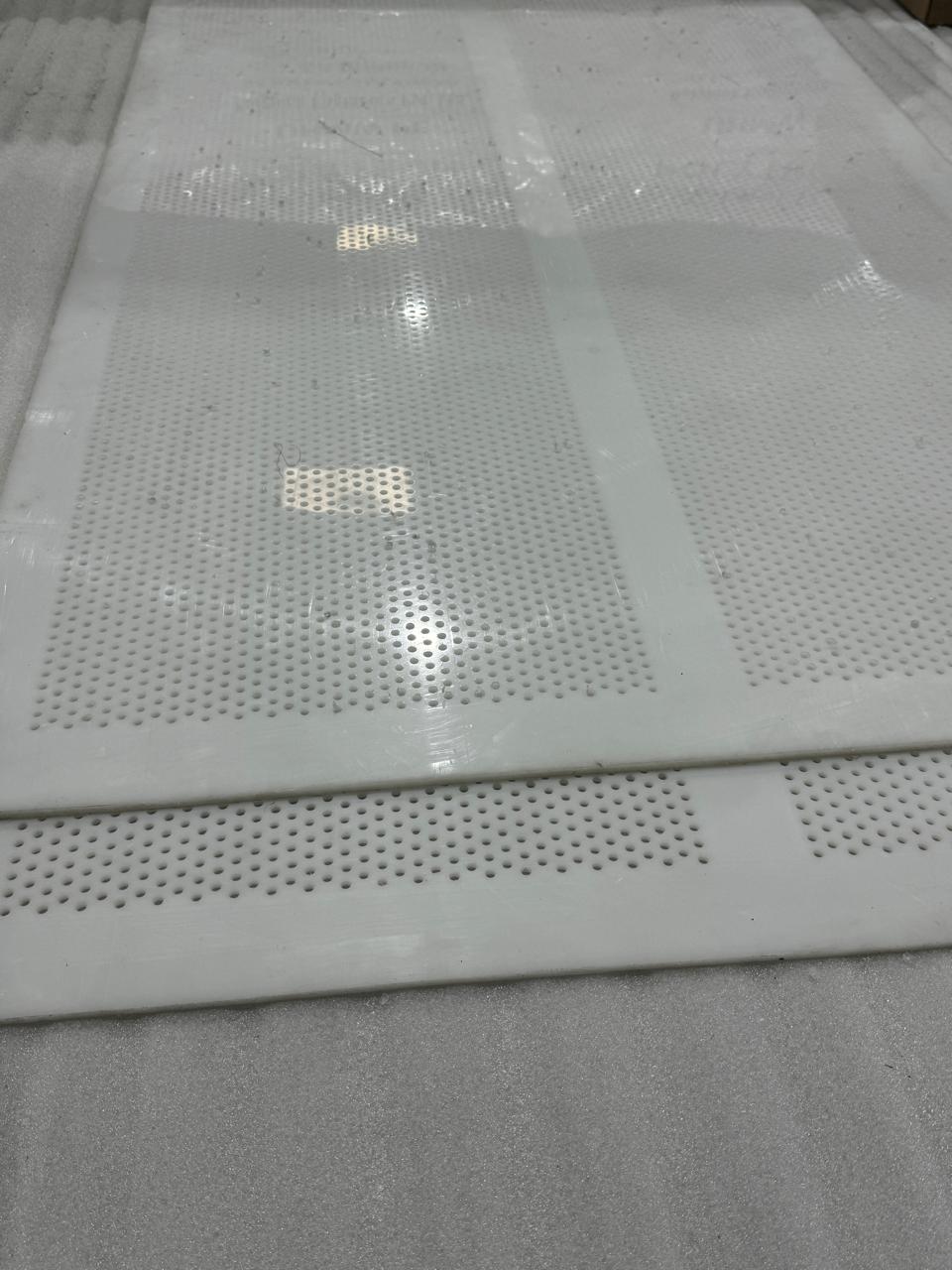
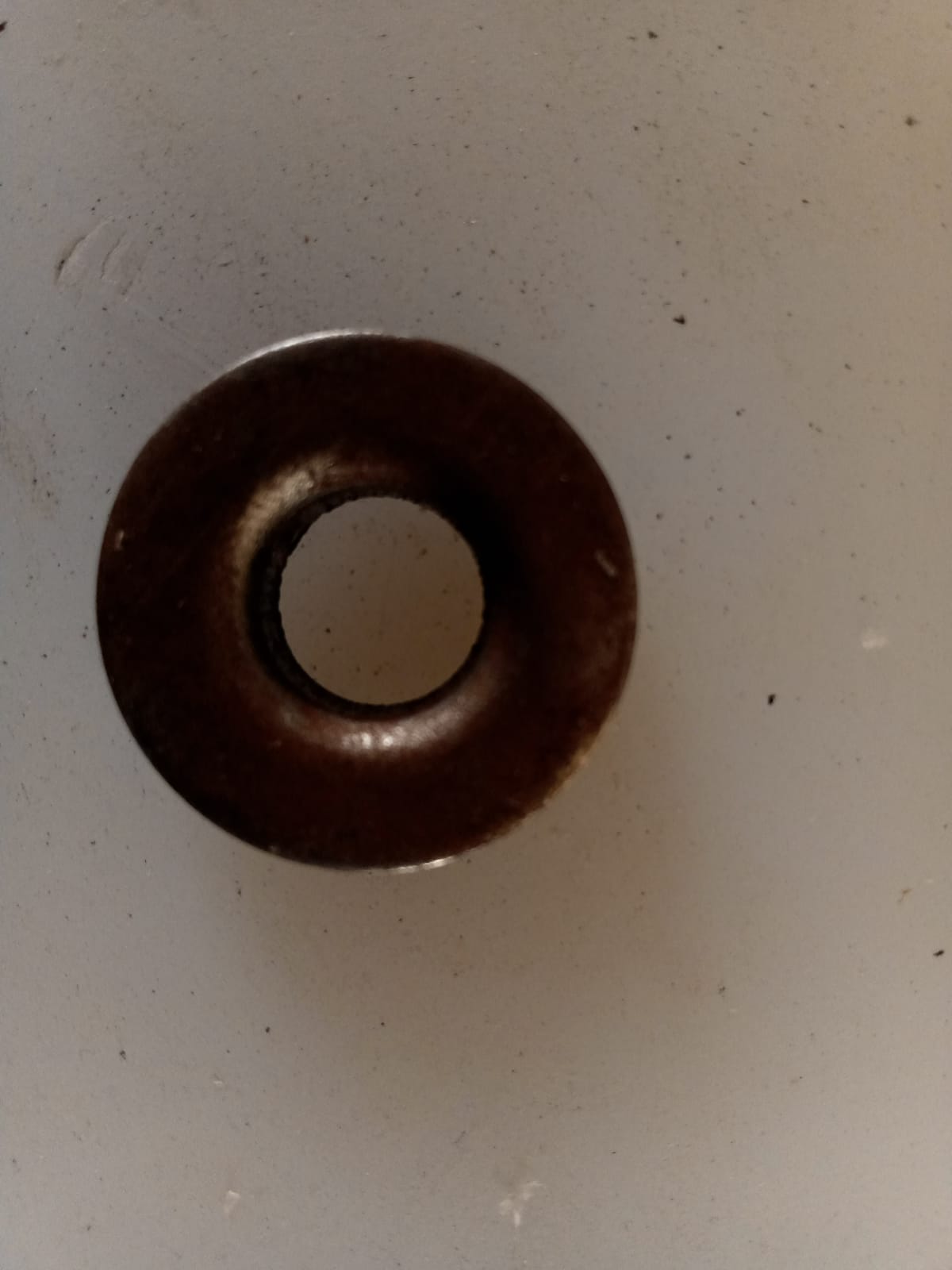
1. Coil Handling and Storage:
a) Coil Saddles:
- UHMW PE pads on coil saddles protect steel coils from damage during storage and
handling.
- They distribute the weight evenly and prevent metal-to-metal contact.
b) Coil Cars:
- Pressure pads on coil cars cushion the coils during transport within the facility.
c) Coil Lifters:
- Pads on coil lifting devices protect the inner and outer surfaces of coils during lifting
operations.
2. Plate Handling:
a) Stacking Systems:
- UHMW PE pressure pads in plate stacking systems prevent scratching and denting of
plates.
b) Plate Separators:
- Pads used in plate separation systems to protect surfaces during handling and storage.
3. Rolling Mill Operations:
a) Entry and Exit Tables:
- Pressure pads on rollers and guides in mill entry and exit tables reduce friction and prevent
marking.
b) Side Guides:
- UHMW PE pads on side guides help control lateral movement of steel without damaging
edges.
4. Finishing Lines:
a) Tension Levelers:
- Pads in tension leveling equipment help distribute pressure evenly across the steel strip.
b) Inspection Tables:
- Pressure pads on inspection tables prevent surface damage during quality checks.
5. Packaging and Shipping:
a) Strapping Systems:
- UHMW PE pads protect steel products from damage during strapping and bundling.
b) Loading/Unloading Equipment:
- Pressure pads on forklifts and cranes protect products during loading and unloading.
6. Processing Equipment:
a) Forming Dies:
- UHMW PE pads used in some forming operations to prevent direct metal-to-metal contact.
b) Clamping Systems:
- Pressure pads in clamping devices for holding steel products during processing.
Benefits of UHMW PE Pressure Pads in Steel Industry:
1.Surface Protection:
- Prevent scratching, denting, and other surface damage to steel products.
2.Load Distribution:
- Evenly distribute pressure to prevent localized stress points.
3. Friction Control:
- Low friction coefficient helps in controlled movement of steel products.
4. Chemical Resistance:
- Withstand exposure to oils, greases, and other chemicals common in steel plants.
5. Durability:
- Long service life in demanding industrial environments.
6. Noise Reduction:
- Dampen noise from metal-to-metal contact.
7. Customizability:
- Can be easily machined and shaped to fit specific equipment needs.
Design Considerations:
1. Thickness and Hardness:
- Selected based on load and application requirements.
2. Size and Shape:
- Customized to fit specific equipment and product dimensions.
3. Surface Texture:
- May be smooth or textured depending on the application.
4. Attachment Method:
- Can be mechanically fastened, adhesive bonded, or designed for easy replacement.
5. Temperature Resistance:
- Selected grade should withstand operational temperatures.
Implementation and Maintenance:
1. Regular Inspection:
- Check for wear, deformation, or damage.
2. Cleaning:
- Periodic cleaning to remove oil, grease, and metal particles.
3. Replacement Schedule:
- Timely replacement to ensure consistent performance.
4. Performance Monitoring:
- Track the effectiveness in reducing product damage and improving handling efficiency.
Limitations:
- Not suitable for extremely high-temperature applications.
- May require more frequent replacement in high-wear applications.
- Load-bearing capacity limitations compared to metal alternatives.
UHMW PE pressure pads in the steel industry contribute significantly to product quality, equipment longevity, and operational efficiency. Their use helps minimize damage to high- value steel products throughout the production and handling processes.